π¨βπ The Beginner's Guide: How to Integrate Machines, MES Software, and People in a Food Factory?
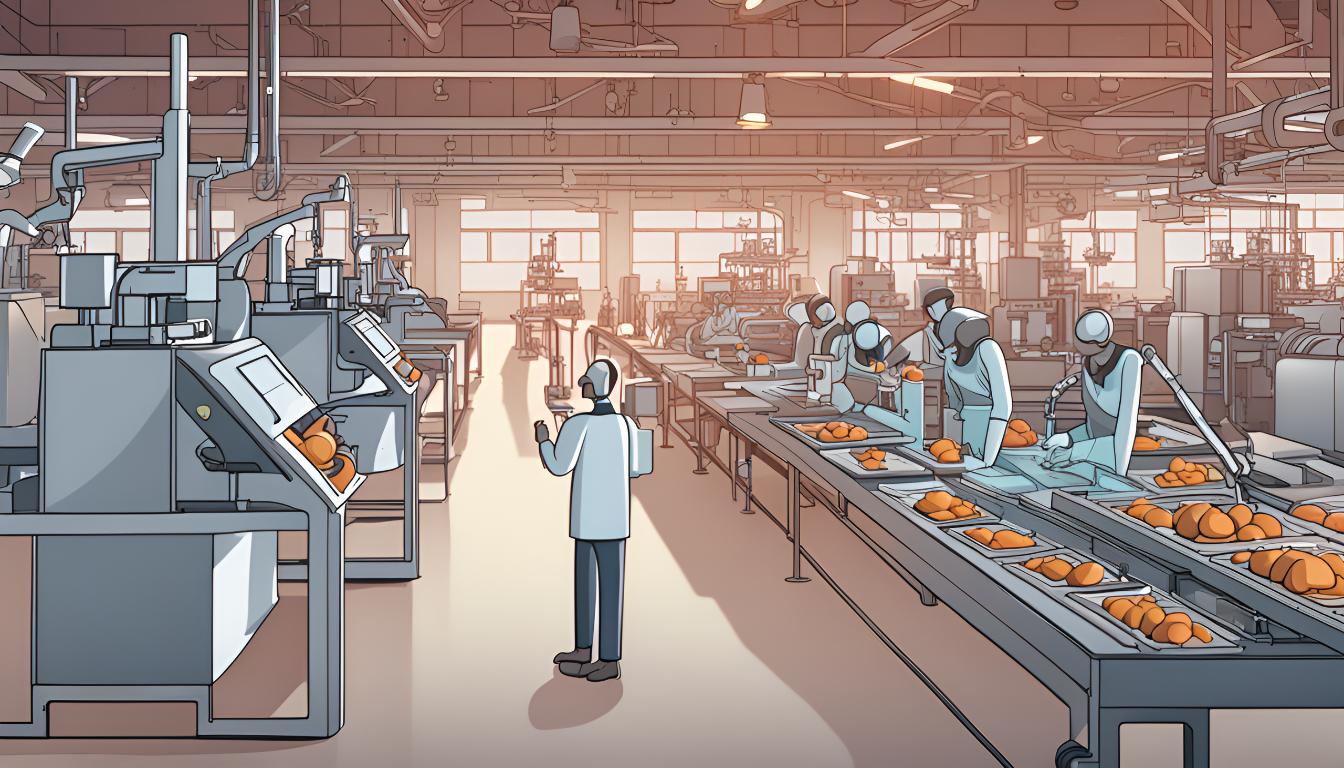
βIntroduction
The food and beverage industry is responsible for taking up 60-70% of the shelf space in most grocery stores! So it's not surprising that it also has one of the widest product varieties in any industry.
Bread, hamburgers, French fries, ice cream, beer, milk, and the list goes on... What most people ignore is that producing beer, for example, is very different from producing milk. Producing hamburgers is very different from producing french fries. For example, while French fries like Lay's or Pringles are produced on fully automated production lines, hamburgers are likely to involve a good percentage of manual labor.
To help the industry become more efficient, machine manufacturers such as Marel, MEYN, Bizerba, ESPERA, Buehler and others, have developed machine portfolios that can automate most of what can be efficiently automated in food factories. But there are still obvious limitations to the value that machines alone can bring to the actual factory floor. Most machines don't communicate with each other. Much less with machines from other brands.
This article aims to provide plant managers with a quick guide about how they can start integrating software and machines to drive factory efficiency upwards.
.jpeg)
The Role of Machines in the Food Industry
Although the Food Industry still relies heavily on manual labor, machines play a fundamental role. From slaughter operations, to cutting, transporting, mixing ingredients to packaging finished products, the machines allow faster production cycles and guarantee timely deliveries to satisfy consumer requirements. Automating repetitive tasks improves accuracy, reduces errors, and minimizes manual intervention. These machines are at the heart of the modern food industry, allowing companies to scale operations, maintain quality standards and optimize their global production.
What are the major machine brands in the food industry?
There are several machine brands in the food sector, known for their cutting-edge technology and reliability. These brands offer a wide range of machinery adapted to various production needs, ensuring efficiency and quality in food processing. Adopting innovative solutions from these leading manufacturers can significantly improve operational performance and optimize production processes in the food industry.
Here are a few to keep in mind:
What are the main types of machines used in the food industry?
Conveyor mats, mixers, cutters, and packaging machines are among the main types of machines used in food manufacturing processes. These machines play a crucial role in optimizing production efficiency and maintaining quality standards. Additionally, filling, sealing, and labeling machines are vital in the packaging phase, ensuring that products are properly sealed and labeled for distribution. The implementation of these various types of machines helps food manufacturers to optimize their production processes and to deliver high-quality products to the market.
Main challenges in the use of machines in the food industry
For food producers with multiple processes and production lines, there are some challenges worth mentioning when working with machines in a highly optimized environment.
Navigating the decision tree in the tables above can be a big challenge. Which brand, which machine is most suitable for a particular plant and process?
How to manage all output data from multiple machines/brands properly and usefully?
In addition, having multiple machines and brands will almost invariably bring different interfaces, user experiences, and operational logic. And they will all need to be taught and mastered. But in one of the industries with the highest employee turnover - yes, food - this means an enormous cost in training the workforce that is lost every year.
Finally, if a worker falls ill, they will alert Human Resources about the problem, how long it will take approximately to recover. That's not the case with machines. Machines rarely βwarnβ. A specialized team will probably have to travel to the site to resolve the issue, which may take days or weeks.
The Role of a Manufacturing Execution System in the Food Industry
Factory Management Software (MES solutions) plays a fundamental role in optimizing production processes in the food industry. With real-time data analysis, these systems improve visibility and scalability, allowing for quick decision-making. The transition to cloud technology offers agility and cost efficiency, while ensuring regulatory compliance. The MES Cloud Software effectively optimizes operations across all production units. By taking advantage of cloud service providers like AWS, food manufacturers can minimize downtime and boost operational efficiency.
.jpeg)
The Evolution of MES: From On-Premise to the Cloud
Manufacturing Execution Systems (MES) transitioned from on-premise to MES Cloud Software, revolutionizing the industry. Cloud technologies provide real-time visibility, scalability, and agility to MES systems. Moving away from traditional on-premise configurations, MES cloud solutions provide greater flexibility and accessibility. This evolution meets modern production processes, ensuring optimized operations and greater efficiency. Adopting cloud-based MES aligns with the industry's shift toward digital transformation and empowers production units with advanced features.
Cloud-Native MES vs Cloud-Based MES
A Cloud Manufacturing Execution System can be of two types: Cloud-Native MES and Cloud-Based MES. They differ in their architecture and implementation approach. While Cloud-Based MES depends on existing cloud infrastructure, Cloud-Native MES is specifically built for the cloud environment, offering more scalability, agility, and flexibility. Cloud-Native MES solutions are designed to take full advantage of cloud technology, providing access to real-time data, improved visibility, and easier regulatory compliance. In contrast, Cloud-Based MES may require more customization for cloud compatibility. Understanding these distinctions is crucial when selecting the right MES solution for your food plant.
Connecting Everything: Software, Machines, and People
In the midst of the intricate network of production processes, IoT emerges as the central element connecting software, machines, and personnel seamlessly. By taking advantage of IoT protocols, companies transcend physical barriers, ensuring real-time visibility and improving scalability. Overcoming integration challenges, IoT promotes a harmonious network where data flows effortlessly, optimizing operations and reinforcing agility. In this interconnected realm, ensuring smooth integration of equipment and addressing security concerns of the MES cloud becomes imperative for sustained efficiency and cybersecurity.
How to Set Up Communications Between Machines and Software?
When designing a system to configure communication between machines and a cloud-native Manufacturing Execution System (MES) or Manufacturing Operations Management (MOM), selecting the correct protocols is crucial to ensure efficiency, scalability, and reliability. The protocols used must support real-time communication, data integrity, security, and compatibility with the cloud.
Here's a table of some of the best communication protocols categorized by their application and cloud integration and MES/MOM systems:
How to Overcome Some Common Machine Integration Challenges?
The integration of machines and software presents several challenges in the food industry. Common obstacles include ensuring compatibility between different technologies, achieving seamless data flow, and maintaining cybersecurity. Overcoming these obstacles requires meticulous planning, robust communication between systems, and adherence to regulatory compliance standards. By taking advantage of cloud technology, companies can improve visibility, scalability, and agility while mitigating downtime risks. Partnerships with experienced cloud service providers such as AWS can optimize the integration process and pave the way for a more efficient and interconnected production environment.
Practical Steps to Ensure Smooth Machine Integration
Establish a clear integration plan outlining objectives and schedules. Perform complete compatibility checks between machines and sensor systems. Implement robust security measures for data protection. Use standardized communication protocols for trouble-free connectivity. Perform comprehensive tests and pilot runs before full implementation. Ensure continuous monitoring for any post-integration issues. Collaborate closely with vendors and internal IT teams for support. Regularly update and maintain all integrated systems for optimal performance.
Benefits of Managing Food Plants with Cloud-native MES
Improving efficiency and reducing manual workload, real-time data analysis for better decision-making, longer uptime compared to legacy systems, converting CapEx expenses to OpEx, flexibility for an M&A-intensive industry, and better integration, development, and workforce retention rates are some of the key benefits of total factory automation with cloud-native MES solutions. This modern approach offers agility, scalability, and improved visibility, revolutionizing production processes and supply chains for optimal performance and regulatory compliance.
Improving Efficiency and Reducing Manual Workload
By integrating machines with MES cloud solutions, food production processes are optimized, significantly reducing manual workload. Real-time data analysis allows for quick decision-making, increasing efficiency. This automation minimizes downtime, improving overall productivity. With cloud technology, scalability and agility are achieved effortlessly, adapting to changes in demand without problems. By taking advantage of these innovative solutions, manual tasks are minimized, freeing up the workforce for more strategic functions, ultimately increasing operational efficiency in the food industry.
Real-Time Data Analysis for Better Decision Making
Leveraging real-time data analysis in food production allows for agile decision-making, quickly optimizing processes. Cloud-native MES solutions facilitate this by offering instant visibility of production data, allowing for timely responses. By harnessing the power of cloud technology, manufacturers can improve efficiency through data-based insights, improving overall operational performance. The integration of real-time analysis with machine data ensures proactive adjustments, driving continuous improvement within production environments. This strategic approach improves adaptability and responsiveness to dynamic market demands, fostering a competitive advantage.
Longer uptime compared to legacy systems
Cloud-native MES solutions offer longer uptime compared to legacy systems in the food industry. By taking advantage of cloud technology, real-time data analysis, and scalable infrastructure, downtime is minimized. This ensures continuous operation of production processes, improving efficiency and reducing manual intervention. With better visibility and agility, cloud MES systems outperform legacy MES systems by providing uninterrupted services, ultimately optimizing production units and improving overall performance.
Convert CapEx Expenses to OpEx
By integrating machine integration technology, food manufacturers can convert capital expenditures (CapEx) into operating expenses (OpEx). This change allows for better budget management by distributing costs over time instead of large initial investments. Cloud-based MES solutions and SaaS platforms offer scalability and agility, allowing companies to adjust resources based on demand. This financial strategy provides flexibility in spending, aligning costs with production needs while improving overall operational efficiency.
Total Flexibility for a Highly M&A Intensive Industry
In a highly M&A-intensive industry, the flexibility offered by cloud-native MES solutions is unmatched. The agility and scalability they provide perfectly match the dynamic nature of mergers and acquisitions. With cloud technology, integrating new production units or supply chains becomes simple. This flexibility ensures minimum downtime during transitions, offering uninterrupted visibility into all processes. By taking advantage of cloud solutions, companies can navigate regulatory compliance effortlessly, making mergers and acquisitions smoother and more efficient.
Better Workforce Integration, Development, and Retention Rates
Improving labor force integration, development, and retention rates is crucial in the dynamic food industry landscape. By using cloud-native MES solutions, companies can optimize training processes, provide real-time feedback, and offer customized development paths. This leads to a qualified and engaged workforce, reducing turnover rates and improving operational efficiency. With improved visibility and agility through cloud technology, employees are better equipped to adapt to evolving production processes, contributing to overall business success.
Conclusion
In conclusion, integrating machines with a cloud manufacturing execution system changes the way factories work for the better. It helps improve efficiency and decision-making, increase productivity, and reduce the amount of manual labor required. They also get real-time data to help make better decisions. Switching to cloud-based MES solutions means more uptime, a shift from CapEx to OpEx spending, and better connections between facilities, subcontractors, and customers. Focusing on microservices and cloud-native design, this change opens up many new opportunities for easy machine integration and IoT-based predictive maintenance. This leads to smoother operations and stronger cybersecurity.
β
Learn how BRAINR's cloud-native MES software can help you achieve full machine integration in your factories!
β
β