Inventory Management Under Pressure: How Medium and Large Food Companies Lose Money Without a WMS
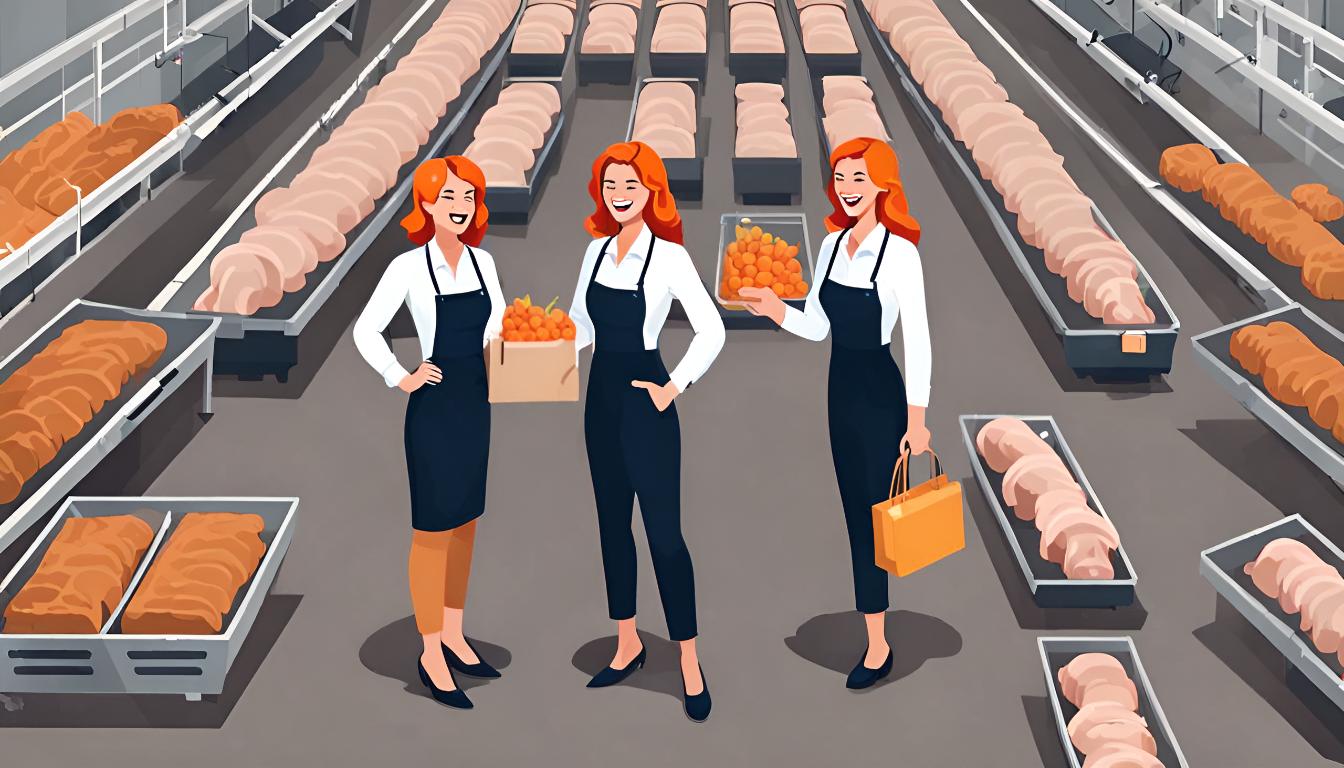
The world of food companies has always faced a challenging scenario, especially when it comes to managing inventory and warehousing. Without an effective warehouse stock management system, these companies may see their profits evaporate. According to 2023 McKinsey Global Logistics Survey, poor inventory management can cause significant erosion of profits. So let's understand how to avoid these pitfalls?
Common Inventory Management Problems in Midsize Companies
Many mid-sized businesses deal with issues such as incorrect inventory counts and excess or lack of stock on a daily basis. Products that are forgotten and exceed their expiration date or the lack of key items at critical moments are common scenarios. Additionally, reliance on manual processes to manage inventories can lead to human errors, such as duplicate or forgotten counts. Ineffective communication between departments can also result in purchasing decisions based on outdated data, compounding stock management problems. These challenges not only affect daily operations, but can also have significant financial impacts. According to Forrester, inefficiencies in the supply chain and inventory management cost around 1.1 trillion dollars annually. In addition to direct financial costs, these failures can lead to a loss of trust from customers and business partners, affecting the company's reputation in the market. Another common problem is the difficulty in predicting product demand, which can result in an excess stock of low-turnover items and a lack of stock of high-demand products. The lack of real-time visibility over inventory levels also contributes to the inability to respond quickly to changes in the market or to unexpected problems in the supply chain. Without a robust system to manage these challenges, companies risk losing growth opportunities and facing ongoing financial difficulties.
How Inefficiencies Cost Money
These inefficiencies can cause significant damage to a company's finances over time. Incorrect inventory counts and outdated data result in wrong purchasing decisions, leading to stock ruptures that cause lost sales and dissatisfied customers, or excesses that increase storage costs and can lead to waste, especially in perishable products. The lack of a real-time inventory management system makes it difficult to quickly adjust stock levels to demand fluctuations, increasing the likelihood of errors.
In addition, the dependence on manual processes can generate a series of additional problems, such as human errors and communication failures between departments, which can delay the production and shipment of products. Ineffective communication can result in outdated data, exacerbating inventory problems and leading to inefficient resource allocation.
For example, a company that is unable to effectively forecast demand may end up with an excess of low-turnover products that take up valuable warehouse space and immobilize capital that could be better used. On the other hand, the lack of high-demand products can lead to a loss of sales and, eventually, of customers to the competition. Supply chain inefficiencies can also affect a company's ability to respond to changes in the market, which can limit growth and innovation capacity.
Implementing an efficient inventory management system can minimize these inefficiencies, allowing for better resource allocation, improving inventory visibility, and ensuring that stock levels are always optimized to meet demand.
Implementing a WMS as a Solution
The implementation of a WMS (Warehouse Management System) can be a true turning point for medium and large food companies. This system allows real-time monitoring, automation in inventory management and optimization of stock levels, resulting in more efficient and profitable operations. With a WMS, companies can automate manual tasks that were previously prone to errors, such as counting inventory and updating records, ensuring data that is always accurate and up-to-date. Automation also allows for a faster response to demand fluctuations, helping to avoid both stock outages and excesses.
The real-time visibility offered by a WMS is crucial for identifying and resolving problems immediately. Centralized information accessible to all departments facilitates communication and coordination, eliminating errors and delays caused by outdated or miscommunicated data. Additionally, a WMS can provide detailed analyses and reports, allowing for more informed and strategic decision-making.
Introduction to BRAINR
BRAINR is a cloud-based MES/MOM solution designed specifically for the food industry. Not only does this system facilitate automated and real-time inventory management, it is also optimized to ensure compliance with strict food safety regulations, such as IFS or HACCP. One of the great advantages of BRAINR is its ability to integrate and centralize information from different departments, providing complete and instant visibility of the entire operation. This allows for more informed and agile decision-making, essential for maintaining competitiveness in a dynamic market.
The platform offers advanced tools to monitor performance and identify areas for improvement, from receiving raw materials to shipping finished products. The ability to accurately forecast demand helps to adjust stock levels, minimizing both excess and lack of products. With BRAINR, it is possible to automate critical processes, reduce human errors, and increase operational efficiency, resulting in significant savings and greater customer satisfaction.
In addition, BRAINR is highly scalable, making it suitable for companies of different sizes and operational complexities. The implementation is simplified thanks to its cloud architecture, allowing for rapid adoption without the need for large investments in infrastructure. BRAINR's flexibility and robustness make it an ideal choice for any food company seeking to optimize its inventory management and ensure compliance with food safety regulations.
Impact on the Real World
A practical example of BRAINR's effectiveness is the Lusiaves Group who decided to implement BRAINR to, among others, optimize its inventory management. Prior to implementation, the company faced significant challenges, such as difficulty maintaining adequate stock levels and over-reliance on manual processes, which resulted in frequent errors and operational inefficiencies.
Following the adoption of BRAINR, the company witnessed an impressive transformation in its warehouse operation. The real-time monitoring capacity and the automation of processes have drastically reduced human errors. In just six months, the company was able to reduce inventory discrepancies by 40%, which translated into substantial savings and better resource utilization. In absolute terms and only at a Lusiaves Group plant in central Portugal, in less than half a year, the Group “earned” more than 4 million euros in unknown stock!
In addition, the company was able to forecast demand more precisely, adjusting stock levels as necessary and avoiding both excess and lack of products. This precision allowed for a more agile response to market changes and improved customer satisfaction, who could now rely on the constant availability of products.
Operational efficiency increased by 30%, allowing the company to focus on other strategic areas for its growth. This real case illustrates how BRAINR can transform inventory management and drive the success of food companies.
How to take action?
If these inefficiencies sound “familiar”, it's time to consider BRAINR as the solution to avoid costly waste and boost growth. In a sector as competitive as the food sector, investing in an automated and real-time inventory management system is essential to maintain competitiveness and ensure customer satisfaction. The implementation of a WMS like the one offered by BRAINR is transformative, providing complete and instant visibility of stock levels, automating manual processes and improving the accuracy of demand forecasts. It's not just about improving operational efficiency, but also about creating a solid foundation for sustainable growth. If you are interested in learning more, simply schedule a first discussion with BRAINR.